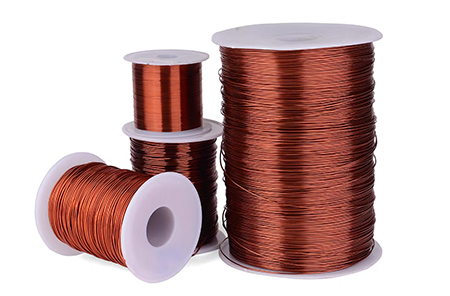
180 Class Polyesterimide Enameled Aluminum Round Wire
Polyesterimide enameled aluminum round wire has a heat resistance class of 180°C and withstands a thermal shock temperature of 200°C. The enamels are primarily based on polyurethane, providing a high cut-through temperature, excellent solderability, and outstanding pinhole performance in alcohol or salty water. The polyesterimide enameled wire complies with IEC 60317-0-3 and IEC 60317-15 standards and has obtained UL certification.
- Exhibits good film toughness and scratch resistance, suitable for automatic winding and embedding.
- Demonstrates excellent thermal shock and outstanding softening breakdown performance, suitable for high-temperature, overload, and heavy-duty motor and electrical products.
- Possesses excellent thermal stability and solvent resistance, withstanding the majority of organic solvents.
Specification of polyesterimide wire enamel
Enamelled Round Wire Conductor Diameter: Class 1 Conductor 0.4-1.6mm; Class 2 Conductor 0.4-5.0mm
Enamelled Round Wire Film Thickness (both sides): Class 1 Film 0.05-0.08mm; Class 2 Film 0.12mm; Extra Thick Film 0.45mm;
Enamelled Round Wire Diameter Range: Standard Sizes Ø0.2-6.0mm; Maximum Size Ø3.0-15.0mm
Enamelled Rectangular Wire Size Range:
Standard Sizes: a: 1-5.6mm, b: 2.0-16.0mm;
Maximum Sizes: a: 2.0-3.5mm, b: 16.0-35.0mm;
Film Thickness Grades: Class 1, Class 2, Class 3
Solvent Resistance: Standard solvents, "H" hardness pencil does not scratch the insulation layer
Surface: Dark red, smooth, glossy, without coating
Spools: PT25, PT30, PT35, PT60, PT90, PT200, PT270 wooden spools, each reel can weigh up to 150kg, and conical spools or other spool types are available, with models customized according to customer requirements.
Click to view Signi enameled wire reel specifications
Click to view the technical parameter table of Signi enameled wire
Performance characteristics of polyesterimide wire enamel
General Introduction | Heat resistance | Electrical performance | Mechanical behavior | ||||
---|---|---|---|---|---|---|---|
Standard | NEMA MW 30-C IEC60317-8 GB/T6109.5 | Temperature index (°C) | ≥180 | Film continuity standard requirement (Low pressure G1 0.050mm) | ≤6 | Elongation standard(0.050mm) | ≥10% |
Diameter | 0.016-0.800 | Softening breakdown temperature (°C) standard requirement | ≥300 | Typical value (G1 0.050mm) | 0 | Typical value (0.050mm) | 20% |
Temperature index (°C) | 180 | Typical value (°C) (0.050mm) | 350 | Standard requirements (IEC) (High pressure G1 0.250mm) | ≤40 | Elongation standard(0.250mm) | ≥22% |
Softening breakdown temperature (°C) | 300 | Thermal shock temperature (°C) standard requirement | 200 | Typical value (High pressure G1 0.250mm) | 1 | Typical value (0.250mm) | 35% |
Thermal shock temperature (°C) | 200 | Typical value(0.050mm) | 230 | Breakdown voltage per micrometer | |||
Solderability | Not weldable | Typical value(0.250mm) | 230 | Typical value (0.050mm) | 200 |
Hot selling product
-
Polyimide Enamelled Aluminum Round Wire
Diameter: 0.2-15mm
Flattening Rate: 25-45%
Good Weldability
-
Polyimide Enamelled Rectangular Wire
a Size: 0.08-2.0mm
b Size: 2.0-16.0mm
Tighter Wire Packing
-
Extra Large Polyimide Rectangular Wire
a Size: 2.0-3.5mm
b Size: 16.0-35.0mm
Better Heat Dissipation
Advantages of polyesterimide wire enamel
- High Heat Resistance: Polyimide enamelled wire performs well in high-temperature environments, making it suitable for equipment like motors and transformers that operate at elevated temperatures for extended periods.
- Excellent Chemical Resistance: Polyimide materials typically exhibit outstanding resistance to chemicals, with the ability to withstand the corrosive effects of chemical substances. This ensures stable electrical performance even in chemically harsh environments.
- Superior Coating Performance: Signi utilizes mold coating, ensuring the uniform application of the enamel coating on the conductor. This enhances the insulation layer's uniformity and quality, thereby improving electrical insulation performance.
- Good Thermal Shock Resistance: Good thermal shock resistance means that polyimide enamelled wire can maintain its physical and electrical properties when subjected to sudden high-temperature shocks, preventing damage from thermal shocks.
- Large Thermal Shock Margin: Thermal shock margin refers to the material's tolerance to rapid temperature changes. Polyimide enamelled wire has a large thermal shock margin, allowing it to maintain stable electrical performance in situations involving rapid temperature fluctuations, reducing damage due to temperature changes.
- Excellent Solderability: Good solderability implies that the enamelled wire performs well during the soldering process, making it easy to connect with other electrical components and ensuring reliable electrical connections.
Applications of polyesterimide wire enamel
- Various industrial motors, especially suitable for high-temperature, heavy-duty industrial motor coils.
- Electric tools and non-sealed household appliance motors.
- Dry-type transformers.
- Electronic transformers and power supplies.
- Instrumentation coils in high-temperature environments.
Signi's wire enamel quality control system includes
- Raw material inspection: Rigorous standards are applied to select high-quality aluminum rods, ensuring the base material's superior quality. This step is fundamental to ensuring the performance and reliability of the final product, as the quality of the aluminum rods directly affects the end product.
- Drawing inspection: Emphasis is placed on the high quality and reliability of the insulated conductor. This involves precise selection of raw materials, considering not only the production process but also meeting design specifications to satisfy customer requirements.
- Semi-finished product production inspection: Before coating, processes like drawing (for round wire) or flattening (for rectangular wire) are employed to adjust the dimensions of the conductor (copper or aluminum). This step ensures the uniformity of the conductor and compliance with specifications, providing a solid foundation for subsequent enamel coating.
- Finished product inspection: Particular focus is given to ensuring the quality of winding wires, the most critical part of the product where no compromises can be tolerated. Signi adheres to recognized IEC standards as the minimum quality benchmark to ensure that each finished product meets internationally accepted quality standards.
- Packaging and labeling inspection: The production is integrated with a reviewed quality control system to ensure that product packaging complies with specifications. This is supported by a well-trained technical team and fully equipped laboratory facilities.
- Up to 13 testing items: To ensure the reliability of wire enamel in its final use in motors, transformers, or coils, Signi conducts up to 13 testing items. With a comprehensive quality control and packaging system, the company ensures that any product issues can be traced and provides customers with a more reliable guarantee.
Signi enameled wire related products
-
130/155 Class Polyester Enameled Aluminum Round Wire
Temperature Resistance: Class 130
Thermal Shock Resistance: 150°C
-
200/220 Class Enameled Round Aluminum Wire
Temperature Resistance: Class 200/220
Thermal Shock Resistance: 240°C
-
240 Class Polyester Enameled Aluminum Round Wire
Temperature Resistance: Class 240
Thermal Shock Resistance: 260°C
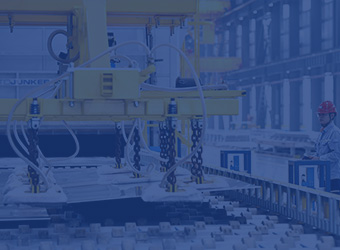